Günümüzde üretim yapan firmalar başta olmak üzere, tüm organizasyon sistemlerinde üretim fonksiyonlarının yürütülebilirliği ve izlenilebilirliğini kolaylaştıracak planlama sistemlerinin kullanılması çok önemlidir. Özellikle bilgisayar destekli imalat yapmak durumunda olan firmaların bu ihtiyaçları daha net görülmektedir. İmalat fonksiyonlarının bütünsel bir yapı olarak gerçekleştirilmesi için kapsamlı planlama çalışmaları yapılmalıdır. İşletmeler bu ihtiyacı karşılayabilmek ve imalat yöneticilerine destek sağlayabilmek amacı ile MRP (Materials Requirement Planning) olarak bilinen Malzeme İhtiyaç Planlaması, MRP 2 (Manufacturing Resource Planning) olarak bilinen İmalat Kaynak Planlaması ve ERP (Enterprise Resource Planning) sistemleri olarak yaygın bir şekilde kullanılan Kurumsal Kaynak Planlaması gibi yaklaşımlar geliştirilmiştir. Bu yazımızda Malzeme İhtiyaç Planlaması ile ilgili biraz bilgi edinmeye ne dersiniz?
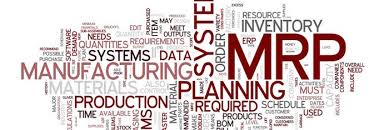
Malzeme İhtiyaç Planlaması (MRP) nedir?
Malzeme ihtiyaç planlaması; firmaların üretim için gerekli malzeme miktarlarının ve zamanlarının belirlenerek en uygun zamanda ve en uygun miktarda sipariş satın almalarının gerçekleştirilmesini sağlamak amacıyla kullanılan bir yönetim çizelgeleme ve kontrol tekniğidir. Birçok firma maliyetlerini azaltmak ve karı arttırmak için MRP sistemlerini kullanmaktadır. Malzeme ihtiyaç planlama sistemleri, stok maliyetlerini düşürmek aynı zamanda programlama etkinliğini geliştirmek ve sektördeki değişikliklere hızlı bir şekilde yanıt verebilmek için imkan sunmaktadır. İşletmeler rekabet ortamında ayakta kalabilmek için kalite ve verimliklerini arttırabilmek amacıyla bu sisteme ihtiyaç duymaktadır. Bir MRP sisteminin başarılı olabilmesi için etkili bir planlama, doğru veri, yeterli bilgisayar desteği, yönetimin desteği ve kullanıcı bilgisi gerekmektedir.
MRP, beklenmeyen durumlarda yeniden planlama ve programlama ile malzeme eksikliklerinin veya fazlalıklarının önlenmesini sağlayacak önceden tahmin yeteneğine sahiptir.
MRP’nin Tarihçesi
1950’lere kadar neredeyse her firma üretim planlaması için stok yönetimi şeklinde basit bir planlama yapmaktaydı. Mevcut hesaplama teknikleri ile her ürün için stok yönetimi yapmak firmalarda kayıplara yol açmaktaydı. 1950’lerde yavaş yavaş gelişmeye ve yaygınlaşmaya başlayan bilgisayarların da yardımı ile daha ayrıntılı üretim planlama yapma fırsatı doğmuş ve üretim planlamada yeni bir teknik olarak malzeme ihtiyaç planlaması geliştirilmiştir. Daha eskilerde stok yönetimi her ürün için bağımsız olarak yapılmaktayken Malzeme İhtiyaç Planlanmasının geliştirilmesi ile artık bir ürünü oluşturan tüm parçaların planlaması yapılabilir hale gelmiştir.
Orlicky’nin 1974 yılında “Materials Requirement Planning” adlı kitabı yazmasıyla, bu yaklaşım imalat planlama ve kontrolde bir devrim olarak niteledirilmeye başlanmıştır.
MRP’nin Avantajları
- Ürün ağacında bulunan nihai ürün ve üretim kapasiteleri ile ilgili planlama yapılmasını sağlar.
- Alt düzey ihtiyaçların belirlenmesini ve belirlenen bu ihtiyaçların zaman planlamasını belirler.
- Kesinleşen sipariş miktarlarının ve satışların takip edilerek gerekli analizin yapılmasını sağlar.
- Üretim planının, ürünün stok miktarının ve kalan miktarın takip edilmesini kolaylaştırır.
- Stok ve depo maliyetlerinin analiz edilebilmesini sağlar.
MRP’nin Dezavatajları
- Malzeme ihtiyaç planlama sistemleri doğru girdi bilgisine güvenir. Bu nedenle stok kayıtları iyi tutulmamışsa veya ilgili tüm değişikliklerle birlikte malzeme faturalarını güncellenmemişse, sistem çıktıları da doğru olmayacaktır.
- MRP ile ilgili diğer dezavantaj ise sistemlerin zor, zaman alıcı ve uygulamanın maliyetli olabilmesidir.
MRP’de Sisteminin Girdileri
Malzeme ihtiyaç planlamasının temel olarak beş adet girdisi vardır. Bu girdiler:
-Ürün ağacı: Bir ürün yatay ve düşey ilişkilerle birbirine bağlı, birçok elemandan oluşan bir ağaç yapısındadır.
-Eldeki stok miktarı: Ürün ağacındaki herhangi bir ürünün, üretime başlamadan önce stokta kaç adet bulunduğudur.
-İhtiyaç miktarları: Planlama dönemindeki tüm alt dönemler için üretilmesi ya da satın alınması gereken miktarlardır.
-Tedarik/Üretim zamanı: Tedarikçilerden temin edilecek ürünler için tedarik süresini veya üretilmesi gereken ürünler için üretim süresini verir.
-Planlanmış alım: Bu miktar bir ürün için daha önce sipariş edilmiş, geliş zamanı belirli miktarlardır.
Şekil 1’de basit bir MRP tablosu verilmiştir. Örneğimizde 5 dönemlik bir planlama yapılmaktadır. İlgili üründen ihtiyaç duyulan ürün miktarları dönem dönem gösterilmiştir. Bu üründen daha önceden sipariş verilmiş ve 1. dönemde sipariş miktarı olan 45 adet ürün gelmiştir. Üretime başlamadan önce gerekli üründen mevcut stokta 15 adet bulunmaktadır. Bir siparişin sisteme gelmesi için 2 dönem geçmesi gerekmektedir. Bu verilere göre stok miktarları her dönem için hesaplanmıştır. Hesaplama; her dönem için bir önceki dönemden kalan stok miktarı ile varsa o dönemde yapılan alım miktarı toplanır ve ihtiyaç miktarı bu toplamdan çıkarılır. 5. Dönemde eldeki stok miktarı ihtiyacı karşılayamamaktadır. Bu nedenle sipariş verilmesi gerekmektedir. Verilen sipariş 2 dönemde geleceği için 5. döneme yetiştirebilmek amacı ile siparişin en geç 3. dönemde verilmesi gerekmektedir.
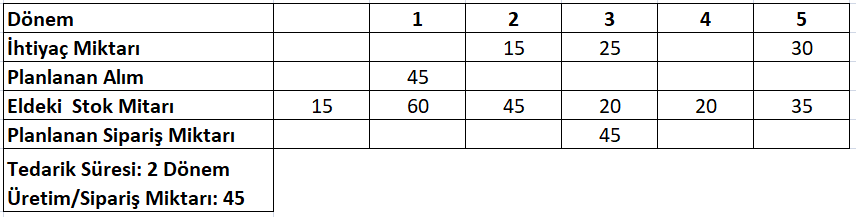
Malzeme İhtiyaç Planlamasında Sipariş Miktarları
Malzeme ihtiyaç planlama sistemlerinde kullanılan sipariş miktarları toplam stok maliyetini en aza indirgeyecek şekilde hesaplanır. Ancak en az maliyeti elde etmek karmaşık bir problemdir; bu nedenle genelde sezgisel yöntemler kullanılır. MRP’de kullanılan sezgisel yöntemlerden bazıları şunlardır:
-İhtiyaç kadar sipariş
-Ekonomik sipariş miktarı
-Dönemsel sipariş miktarı
-En az birim maliyet
-Silver-Meal sezgiseli…
MRP Kodlama Sistemi ve Sistemin Standartları
Malzeme ihtiyaçları planlaması sistemleri çeşitli ön koşullar vardır. Bunların doğru biçimde yapılması sistemden alınacak verimin doğruluğunu belirler. Bu nedenle bir ana plan oluşturulmalıdır. Bu ana plan içerisinde son ürünün ne zaman ve ne kadar miktarda üretilmesi gerektiğini göstermelidir. Kodlama sisteminde üretim aşamasında üretime dahil olacak bütün stoklar kodlanmalıdır. Bu kodlama sistemi açık ve kolay anlaşılabilir olmalıdır. Ürün ağacındaki bütün malzemelerin eksiksiz biçimde listesi çıkarılmalı ve sisteme tanıtımı yapılmalıdır. MRP sisteminin doğru bir şekilde çalışabilmesi için; bütün ürünlerin temin süresi bilindiği, kontrol altındaki bütün stokların sisteme girip çıktığı, seri üretimin yapıldığı alanlarda üretime dahil olacak bütün stok ürünlerinin gerektiği noktada, gerektiği miktarda hazır bulundurulacağı, sistem sayı odaklı çalıştığı için stok ürünlerinin kesikli olarak kullanıldığı, kesikte belirtilen miktarın dışına çıkılmadığı varsayılır. Ayrıca Malzeme İhtiyaçları Planlama sistemlerinde stokların bağımsızlığı esastır. Yatırımları düzenleyip müşteri odaklı çalıştığı için MRP sistemi işletmeler tarafından ilgi görmektedir.
Bir sonraki yazımızda MRP 2 olarak bilinen İmalat Kaynak Planlamasına değineceğiz.
Bilgiyle kalın..
Kaynakça
1. https://www.muhendis.tv/malzeme-ihtiyac-planlamasi-mrp-nedir-kullanim-amaclari-nelerdir
2. http://www.prowmes.com/blog/malzeme-ihtiyac-planlamasi-mrp-nedir/
3. https://mavvo.com.tr/blog/urun-agaci-nedir/
4. https://www.akinsoft.com.tr/kurumsal-kaynak-planlamasi/mrp-programi.php
5. https://www.modelerp.com/makaleler/mrp-nedir/.html
6. https://bilisim.com.tr/blog/malzeme-ihtiyac-planlama-mrp-nedir-kullanim-alanlari-nelerdir/
7. https://www.dia.com.tr/malzeme-ihtiyac-planlamasi-nedir/
9. ÖZTEMEL, E. Endüstri Mühendisliğine Giriş. İstanbul: Papatya Yayıncılık, 2015.
10. YENERSOY, G. Üretim Planlama ve Kontrol. İstanbul: Papatya Yayıncılık, 2015.