Teknolojinin ilerlemesiyle günümüz dünyasında, işletmelerin devamlılıklarını sürdürebilmeleri için kendilerini ve üretmiş oldukları ürünlerin kalitesini sürekli iyileştirmesi temel hedefleri haline gelmiştir. İşletmeleri bu hedeflerine ulaştıracak araçlardan biri mamullerin istenilen kalite spefikasyonlarda olması ve varsa mevcut hatalardan arındırılarak prosesin kontrol altına alınmasıdır.
Eskiden kalite kontrol kavramı sadece ölçme işlemlerini içerirken günümüzde bu uygulamalar yerine istatiksel proses kontrol tekniklerine bırakmıştır. İstatiksel proses kontrol yani SPC adını İngilizce ‘Statistical Process Control’ kelimelerinin baş harflerinden almıştır.
İPK, müşteri isteklerinin yerine getirilip getirilmediğine, prosesin bu noktada kendi ürettiği değişkenlik sınırları içinde olup olmamasına karar vermede bir araçtır. İPK, bir ürünün en ekonomik ve yararlı bir şekilde üretilmesini sağlamak, belirli kalite spesifikasyonlarına uygunluğunu ve standartlara bağımlılığı hedef almak, hatalı ürün üretimini en aza indirmek amacıyla istatistik prensip ve tekniklerin üretiminin bütün evrelerinde kullanılmasıdır. Buradaki temel amaç işletme içindeki kusurları tespit etmek ve de kusurlu ürün üretimi gerçekleşmeden önce önlem almaktır.
İPK’ de problemlerin belirlenip çözümlenebilmesi için yedi kalite aracı olarak geçen yöntemlerden yararlanılır. Bunlar:
- Sınıflandırma
- Çetele
- Histogram
- Pareto Analizi
- Neden Sonuç diyagramı
- Serpilme diyagramları
- Kontrol Grafikleridir.
Kontrol Grafikleri:
Kontrol grafikleri; istenilen niteliklerde ürün veya hizmet üretebilmek için prosesin istatiksel olarak kontrol ve analiz edilmesinde kullanılmaktadır. Üretimden belirli ve eşit zaman aralıklarında alınan örneklerden elde edilen ölçüm değerlerinin zaman içerisindeki değişimlerin gösterildiği grafiklere denir.
Kontrol grafiklerinin ilk uygulaması, 1924 yılında Walter A. Shewhart tarafından gerçekleştirilmiştir.
İlgilenilen kalite özelliği ölçülebilir özellikte ise, bu durumda merkezi eğilim ölçülerinden aritmetik ortalama, dağılma ölçülerinden ise değişim aralığı ve standart sapma kullanılır. Merkezi eğilim ve dağılma için kontrol grafikleri “Nicel Kontrol Grafikleri ” olarak adlandırılır. Kalite özelliğinin sürekli ve sayısal olarak ölçülememesi, yani kusur sayısı gibi belli bir olayın gözlem sayısına dayanması durumunda kullanılan kontrol grafiklerine ise “Nitel Kontrol Grafikleri” adı verilir. Aşağıdaki şekilde grafiklerin sınıflandırılması gösterilmiştir.
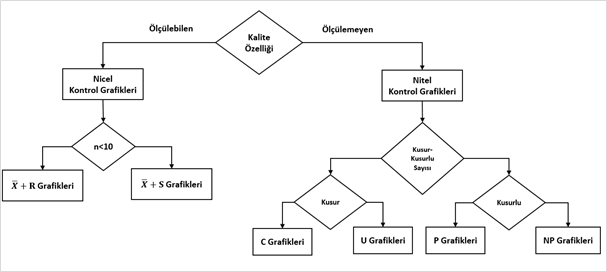
Bir kontrol grafiği esas olarak üç çizgiden meydana gelir. Bunlar; alt kontrol sınırı(AKS), üst kontrol sınırı(ÜKS) ve merkez çizgisidir (MÇ). Kalite özelliğinin ortalama değeri aynı zamanda hedeflenen değer olarak da ifade edilen orta çizgi ile temsil edilir.
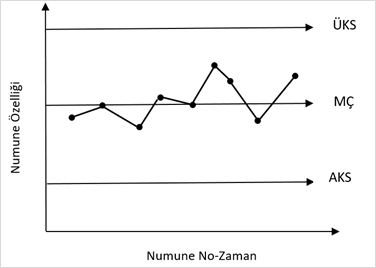
Kontrol grafiğindeki noktalar, sınırların (alt limit sınırı-üst limit sınırı) arasındaysa proses kontrol altındadır ve herhangi bir müdahaleye ihtiyaç duyulmaz. Ölçüm değerlerini simgeleyen bu noktalar arasında bir değişim gözlenir. Bu değişim sistematik bir eğilim göstermedikçe ve kontrol sınırlarını aşmadıkça mevcut bir hatanın varlığına işaret etmez. Kontrol grafiğindeki noktaların en az bir tanesi kontrol sınırları dışında ise sürece müdahale edilip prosesin yeniden incelenerek hatanın tespiti ve gerekli işlemlerin yapılması istenir.
Kontrol grafikleri;
- Prosesteki sapmaları ve prosesin kararlı olup olmama durumunu gösterir.
- Kontrol edilen ürünün kalite karakteristiğinin alt ve üst kontrol limitlerine göre trendini belirler.
- Kalite karakteristiğinin değeri alt ve üst limit değerlerini aşması durumunda bunun nedeninin tespit edilmesi ve düzeltme önlemlerinin alınması gerektiği tespit edilir.
Nitel Kontrol Grafikleri
X(ortalama)- R(Aralık) Kontrol Grafikleri
X-R kontrol grafikleri; kalite karakteristiklerinin ölçülebilen, sayısal olarak ifade edilebilen, değişkenlerde kullanılan kontrol grafikleridir. X kontrol grafiği ortalamadan, R kontrol grafiği ise homojenlikten meydana gelen sapmaları gösterir. X kontrol grafiğinin kontrol sınırları, R kontrol grafiğinin merkez çizgisi kullanılarak oluşturulmaktadır.
X-S Kontrol Grafikleri
X-S kontrol grafikleri, proses ortalamasının ve proses değişkenliğinin kontrol altında olup ol-madığını belirlemede kullanılmaktadır. X kontrol grafiği ortalamadan, S kontrol grafiği ise işletmedeki niceliksel verilerin, işletme ölçüm ortalamasına göre sapmalarını gösterir. Bu sayede prosesteki değişimleri etkin olarak ortaya çıkarmaktadır.
Süreç ortalamasının kontrolünde ortalama olarak ifade edilen X kontrol grafiği, sürecin değişkenliğinde standart sapma için S kontrol grafiği, aralık kontrolü için R kontrol grafiği kullanılır. R ve S kontrol grafiklerinden hangisinin tercih edileceği örneklem hacmine bağlıdır. Örneklem hacminin 10’un altında olması durumunda X ve R kontrol grafiklerinin, 10’a eşit ve üzerinde olması durumunda ise X ve S kontrol grafiklerinin kullanılması önerilmektedir.
P (Kusurlu Oran) Kontrol Grafiği
Ölçülemeyen ancak hatalı-hatasız, red-kabul, geçer-geçmez şeklinde tanımlanan kalite karakteristiklerinin izlenmesinde kullanılır.
NP (Kusurlu Sayısı) Kontrol Grafiği
Kusurlu sayılarını izlemek için oluşturulur. Örnek büyüklüğü sabit olduğu durumda hesaplama ve yorumlama kolaylığı olduğu için kullanılır.
C (Kusur Sayısı) Kontrol Grafiği
Birçok üretim sürecinde ürünlerin bazıları o ürün için belirlenen spesifikasyonların bir ya da daha fazlasını sağlayamayabilirler. Üretilen birimlerin kalite kontrolünde bir birimde rastlanan kusur sayısı esas alındığında c grafikleri kullanılır ( Belli büyüklükte kesilmiş bir kumaş üzerinde boya lekesi vb.)
Muayene edilen birim tek bir üründen oluşabildiği gibi bir grup üründen de oluşabilir (Ör. 10 adet üründen oluşan birim)
U Kontrol Grafiği (Birim Başına Kusur Sayısı)
Muayene edilen birim başına ortalama kusur sayısı esasına dayanır. n birimden oluşan bir örnekte toplam kusur sayısı c olmak üzere, birim başına ortalama kusur sayısı u=c/n olarak bulunur.
Sonuç olarak İstatiksel proses kontrol ile;
- Hatalar kaynağında ve büyümeden önlenir.
- Ürün kalitesine uygunluk sağlanır.
- Hatalı ürün sayısı azalır.
- Maliyet azalır.
- Ürün kalitesindeki farklılıklar azalır, ürüne güven artar.
- Üretim prosesinin şeffaf bir şekilde görülmesi sağlanır.
- Üretim hızı artar.
- Müşteri memnuniyetinde artış ve daha az müşteri şikayeti gözlemlenir.
- İnceleme ihtiyacını azaltılır.
- Hurda, yeniden işleme ve muayene maliyetini azaltılır.
- Daha verimli veri girişi, analiz ve raporlama yapılması sağlanır.
Kaynaklar
1. Elevli, S. (2020). Kalite Kontrol Ders Notları.
2. Aydın B., Arıkan S., İstatistiksel Kalite Kontrol Teknikleri ile Otomotiv Sektöründe Bir Uygulama. Yönetim ve Ekonomi Araştırması Dergisi, 2018.
3. Çolak A., İstatistiksel Proses Kontrolü-Kontrol Grafikleri Çizimi.
4. Patır S., İstatistiksel Proses Kontrol Teknikleri ve Kontrol Grafiklerinin Bir Tekstil İşletmesinde Bobin Sarım Kontrolüne Uygulanması. SÜ İİBF Sosyal ve Ekonomik Araştırmalar Dergisi.
5. Özcan, T., İstatistiksel Kalite Kontrolü Ders Notları.
6.https://endustri.eskisehir.edu.tr/nerginel/TKY302/icerik/N%C4%B0TEL%C4%B0KSEL%20KONTROL%20GRAF%C4%B0KLER%C4%B0.pdf