Bir önceki yazımızda organizasyon sistemlerinde; üretim fonksiyonlarının yürütülebilirliğini ve izlenebilirliğini kolaylaştıracak planlama sistemlerinden malzeme ihtiyaç planlaması ile ilgili bilgi edinmiştik. Özet geçmek gerekirse malzeme ihtiyaç planlaması, bir işletmede istenilen üretimi gerçekleştirmek için gerekli olan malzeme miktarlarının ve zamanlarının belirlenerek en uygun zamanda ve en uygun miktarda siparişlerin gerçekleştirilmesini sağlamaktır. Malzeme ihtiyaç planlama sistemlerinde kapasite gibi kısıtlamalarında dikkate alınması gerekmektedir. Kapasite kısıtlamalarının sisteme dahil edilmesiyle imalat kaynak planlama sistemleri oluşmaktadır. Bu yazımızda malzeme ihtiyaç planlaması ile bütünleşik bir sistem içerisinde yer alan imalat kaynak planlama sitemleri ile ilgili bilgi edinmeye ne dersiniz?
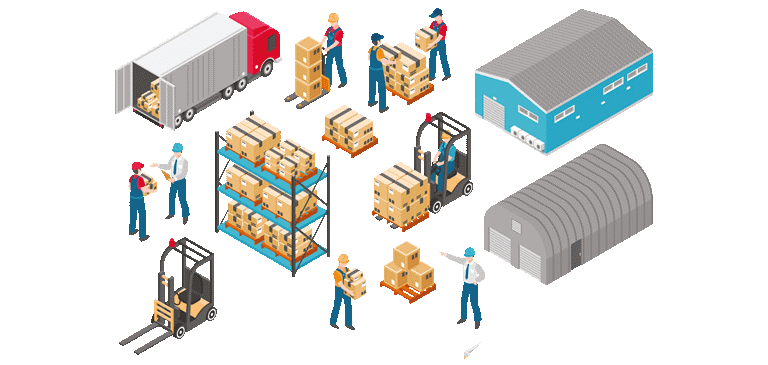
Bilgisayar destekli üretim yapan işletmelerin sayısı gün geçtikçe artmaktadır. Hızla gelişen teknolojiye ayak uydurmak ve teknolojinin avantajlarından faydalanmak adına büyük ölçekli birçok işletme, planlama ve kontrol faaliyetlerini bilgisayar destekli olarak gerçekleştirmektedir. Özellikle imalat kaynak planlama (Manufacturing Resource Planning) yazılımları her gün daha fazla işletme tarafından kullanılmaya başlanmıştır.
İmalat Kaynak Planlaması sistemlerinin temel amacı işletmelerin iş planı, satın alma verileri, yükleme bütçesi, envanter planlarına bakarak stokların azaltılması sağlamak, kapasite kayıplarını önleyecek planlamaların yapılmasını sağlamak, maliyetleri azaltarak ürün kalitesi artırmak ve müşteri beklentilerini verimli bir şekilde karşılamak için yönetim biçiminin değiştirilmesini sağlamaktır.
1980’li yıllarda Malzeme İhtiyaç Planlaması (MRP 1) sistemlerine finans ve simülasyon modüllerinin eklenmesi ile ortaya çıkmıştır. Bu sistem; envanter yönetimi, üretimde çizelgeleme çalışmaları, tasarım mühendisliği ve maliyet kontrolünde etkili karar verme için bilgileri merkezileştirmek, entegre etmek ve işlemek üzere tasarlanmıştır.
İmalat Kaynak Planlaması Bileşenleri
İmalat Kaynak Planlaması, bir işletmedeki neredeyse tüm imalat fonksiyonlarını bütünleşik bir yapı içerinde çalıştırabilmektedir. Sistemin en önemli bileşenleri şu şekildedir:
- Talep Yönetimi: Bir işletmenin ürettiği ana ürün ailesi düzeyinde planlanan satış miktarlarını ve üretim miktarlarını belirtir.
- Üretim Planları: İmalat işletmesi tarafından üretilecek olan ürünlerin ne zaman ve ne miktarda üretileceğine karar verilmesini sağlar.
- Stok Yönetimi: Stok kontrolü ve depolarda bulunan her parçanın stok miktar dengesinin ve statüsünün tutulmasını sağlar.
- Finansman Yönetimi: İşçilik hesaplarının yapılabilmesi, stok maliyetlerinin hesaplayabilmesi, hurda ve iade maliyetlerini hesaplanabilmesi gibi ayrıntılı maliyet hesapların yapılabilmesini sağlar.
- Malzeme ve İhtiyaç Planlaması: Bir ürünü üretmek için gerekli olan tüm hammadde ve ara ürünlerin miktarlarının planlanmasını sağlar.
- Kapasite İhtiyaç Planlaması: Taleplerden hesaplanmış iş emirleri ile gerçek atölyedeki iş yükünü belirler.
İmalat Kaynak Planlamasının Temel Özellikleri
İmalat kaynak planlaması bütünleşik bir yönetim sistemidir. Bir işletmedeki ana üretim için gerekli tüm kaynakların belirli bir düzen içerisinde çalışmasını sağlar. Bu sistem sayesinde veri eksikleri ve tekrarı önlenmeye çalışılır. İmalat kaynak planlama sistemleri işletmenin stratejik, taktik ve operasyonel tüm düzeylerinde kullanılabilecek bir yapıya sahiptir. Bütünleşik yapısı sayesinde işletme içerisindeki tüm birimlerin iletişim ve etkileşim içerisinde olmasını sağlar. İmalat kaynak planlama sistemlerinde ortak veri tabanı kullanılması zorunludur. Fason çalışma olanakları desteklenmektedir. Sistem içerisindeki her bileşenin geri beslenme özelliği vardır. Bu sayede en uygun üretim ortamlarının oluşturulması mümkündür.
İmalat Kaynak Planlaması Girdi ve Çıktıları
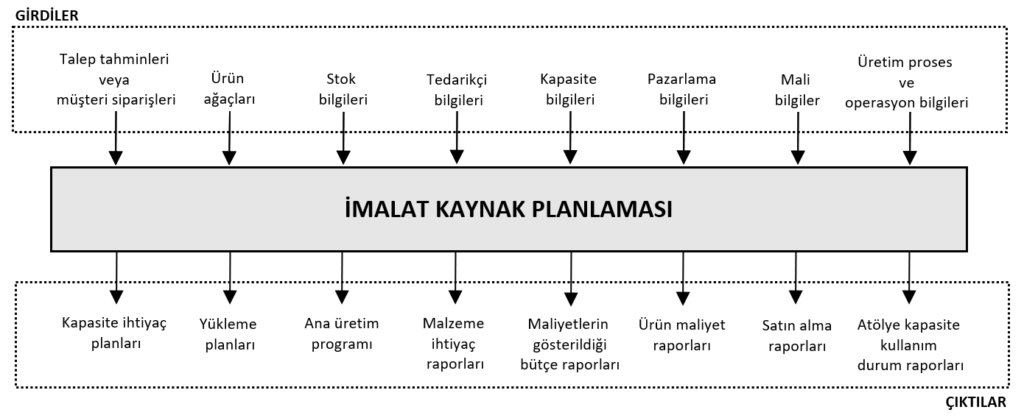
İmalat Kaynak Planlamasının Avantajları
- İşletme içerisinde etkili iletişim ve koordinasyon sistemi kurulmasını sağlar.
- İş yüklemelerinin dengelenmesini sağlayarak fazla mesailerin düzene girmesini ve gereksiz mesailerin ortadan kaldırılmasını sağlar.
- Verimliliklerin görünür bir şekilde hesaplanmasını ve takibinin kolaylaştırılmasını sağlar.
- Satın alma, stokta tutma, yok satma vb. maliyetlerin görünürlüğünü ve azaltılmasını sağlar.
- İşletmelerin otomasyon sistemlerine geçişini kolaylaştırır.
- Makine doluluklarının belirlenmesini ve kullanım oranlarında atış sağlar.
- Kullanılmayan malzeme stoklarını azaltarak stokların dengeli bir şekilde tutulmasını sağlar.
İmalat Kaynak Planlamasının Çalışma Prensibi
Müşteri talepleri ve talep tahminleri ile “Master Üretim Planlaması” yapılır. Üretim planına göre malzeme ihtiyaç planları belirlenir. Malzeme ihtiyaç planları için ürün operasyon planları ve envanter durumu incelenir. Malzeme listeleri belirlendikten sonra sırasıyla parti büyüklükleri ve kapasite ihtiyaçları planlanır. Kapasite ihtiyaçları yeterli değilse master üretim planı tekrar kontrol edilir ve süreç döngüsü oluşur. Kapasite ihtiyaç planları için satın alma gerekli siparişler verirken üretim sahası için tezgah yüklemeleri belirlenir. Son olarak envanter planlama denetimi yapılır.
Bir sonraki yazımızda ERP olarak bilinen Kurumsal Kaynak Planlamasına değineceğiz.
Bilgiyle kalın..
Kaynakça
- YENERSOY, G. Üretim Planlama ve Kontrol. İstanbul: Papatya Yayıncılık, 2015.
- ÖZTEMEL, E. Endüstri Mühendisliğine Giriş. İstanbul: Papatya Yayıncılık, 2015.
- https://blog.mikro.com.tr/uretim-planlamasi-nedir-nasil-yapilir/
- https://www.uyumsoft.com/uretim-planlama
- http://www.mbi.com.tr/makale/mrpi-mrpii-erpii-nedir,5
- https://tr.wikipedia.org/wiki/%C4%B0malat_kaynak_planlamas%C4%B1
- https://www.turkcebilgi.com/imalat_kaynak_planlamas%C4%B1
- https://debis.deu.edu.tr/userweb/sabri.erdem/dosyalar/MRP2_tez_SabriERDEM.pdf
- https://polen.itu.edu.tr/xmlui/handle/11527/17488