Zaman kavramını aklımızda canlandırırsak sürekli değişen dakikalar, saatler hatta aylar, yıllar aklımıza gelir. Zaman değişimin ta kendisi olduğu gibi, rekabeti de arttıran bir kavramdır. Değişen çevre koşulları, teknoloji, bilgi birikimi gibi etkenler, kendilerini güncellemeyen ve hep yerinde saymayı sürdüren işletmeler için katil niteliğinde de diyebiliriz. Şirketler varlıklarını sürdürebilmeleri ve hatta rekabet üstünlüğü sağlayabilmeleri için bazı şartları yerine getirmelilerdir. Bu şartları yerine getirmelerini sağlayacak bir sistemin varlığını biliyoruz. Yalın üretim sistemi olarak adlandırdığımız bu sistem, pazardaki değişime uygunluk sağlayarak, talebe kolay cevap verebilmeyi hedeflemektedir. Bu hedefler doğrultusunda sürekli iyileştirmeyle birlikte israftan kaçınılarak, verimli bir süreç elde edilecektir.
Kaliteden ödün vermeden üretim süresinin kısaltılması, ara stokların eritilmesi, maliyetlerin düşürülmesi sonucu fiyatları düşürme, kaynakları etkili kullanma ve bütün bunların dolayısıyla faydayı arttırma gibi olgular üzerinde yoğunlaşmanın gerekliliği tartışılamaz. Yalın üretim, müşteriye sattığınız ürün ya da hizmetin değersiz kısmının ortadan kaldırılmasıyla ilgilenir. Müşteri de kendisine sağlanacak faydayla ilgilendiği gibi bu faydaya yönelme eğiliminde olduğu için, yalın üretime odaklılık işletmelere büyük kazançlar sağlayacaktır. (Yalın üretim hakkında daha fazla bilgi için sitemizdeki “Yalın Üretim Teknikleri 1 ve 2” yi ziyaret edebilirsiniz. 🙂 )
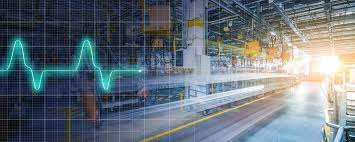
Yalın üretime adapte olabilmek için firmaların öncelik vermesi gereken tekniklerin başlarında kesinlikle değer akışı haritası gelmektedir. Yalın üretimin değerle ilgilendiğini bildiğimize göre, değer akışı haritalamanın nedenini daha iyi bağdaştırabiliriz. Yalın iyileştirmeyi mümkün kılmak için yapılan bu şemalama tekniği ile bütünü ele alıyoruz. Tek bir prosesle ilgilenmek yerine, tamamına odaklandığımızda iyileştirmenin nereden başlayacağına karar verebilmemiz mümkündür. Ayrıca malzeme akışının yanı sıra, bilgi akışı da sağlanmaktadır. Böylece seçilen ürün grubuyla ilgili malzeme ve bilgi akışının haritalandırılması işletme açısından oldukça sağlıklı olacaktır. Haritalanma sayesinde süreçteki her türlü adımla ilgili yeterli bilgi sahibi olacağız. Bu da demektir ki hep vurguladığımız “fayda” doğrudan artış gösterecektir
Tedarikçiler, imalat ve müşteriye sevkiyatı kapsayan bir değer akışı içinde, parça ve yarı mamuller için malzeme ve bilgi akış süreçlerinin haritalarının çıkarılması ise “değer akışı haritalandırma” olarak bilinmektedir (Seth ve Gupta, 2005) Değer akışı haritalama tekniği “Toyota Üretim Sistemi” uygulayıcıları tarafından, yalın sistemleri kurmak için uygulama, planlama, geliştirme, sürecinde mevcut ve gelecek veya “ideal” durumları göstermek amacıyla kullanılmaktadır (Rother ve Shook; 1999: 1). Burada bahsi geçen ideal kelimesi, mevcut durumun değer haritasından yola çıkılarak ulaşılması gereken hedefi temsil eder. Şirket vizyonu olarak da düşünülebilir. İyileştirmelerimizin sonucu bizi ideal duruma taşıyacaktır.
Değer Akışı Haritalandırma Adımları:
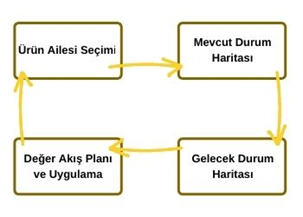
1)Ürün Ailesi Seçimi
Değer akış haritası için gerekli olan ilk aşamada ürün ailesi seçimi gerçekleştirilir. Ürün ailesi ise, üretim yöntemleri benzerliği gibi birbiriyle ortak özellik taşıyan ürünler grubuna verilen addır. Ürün ailesi seçilirken işlemlerde %80 uyum beklenmektedir. O halde aşağıdaki örnekte ürün ailemizin A, B ve C ürünlerinden oluştuğu açıkça görülmektedir.
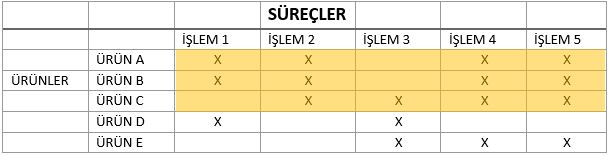
Ürün ailesi seçiminde dikkat edilmesi gereken bazı hususlar vardır. Eğer ki bir işletmede fazla ürün grubu varsa, tüm ürünleri kapsayan bir değer haritası çıkarmak anlamsız olacaktır. Çünkü durumu karmaşıklaştırabilir. Bunu için faydası en büyük olan ürün grubu seçilmesi tavsiye edilir.
Peki faydanın en yüksek olduğu ürün ailesini nasıl bulabiliriz? En fazla üretilen, maliyeti yüksek, üretilmesi güç, pazar hacmi fazla olan ürünler seçimimizde öncelik taşımalıdır. Böylece gerekli düzenlemeler yapıldığında, iyileştirmeleri açık ara farkedebildiğimiz gibi, müşteriye sağlanan fayda da artabilmektedir.
2)Mevcut Durum Haritasını Oluşturma
İyileştirmenin sağlanması için ilk önce mevcut durum verilerinin bilinmesi gerekir. Bunun için baştan başa tüm süreçler ele alınmalıdır. İlk prosesten, müşteriye uzanan sürece kadar tüm adımlar üzerinde analiz yapılmalıdır. Bu analizlerde ele alınması gereken konular vardır;
-Envanter miktarı
-Vardiya süresi ve sayısı
-Operatör sayısı
-Çevrim ve hazırlık süreleri
-Parti büyüklüğü
-Iskarta oranı
-Maliyetler
-Enerji tüketimi gibi bilgilere ulaşılması gerekmektedir.
Bilgi toplama işlemini bizzat sahaya inerek toplamanız daha sağlıklı olacaktır. Bazı veriler önceden kaydedilmiş ve biliniyor olsa bile, doğruluğundan emin olunması gerekmektedir. Seçilen ürün ailesinin üretim adımları boyunca sondan başa (müşteriye ulaşılan prosesten başlangıç prosesine kadar) yürüyerek istenilen verilerin bizzat ölçümü yapılmalıdır. Bu verilerin haritaya işlenmesi için kullanılan bazı evrensel şekiller vardır. Bu şekilleri aşağıdan inceleyebilirsiniz. Çizimler kurşun kalemle yapılması önerilmektedir.
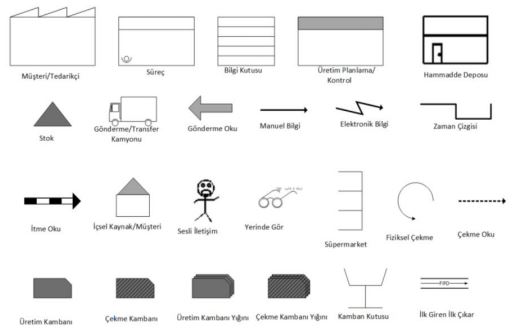
Mevcut durum haritası çiziminin aşamaları şu şekildedir;
İlk adımımızda müşteri ve müşteriye ait verilerin çizimini gerçekleştiririz. Müşteriyi temsil eden bir fabrika sembolü ile altına müşteri bilgilerini yerleştiririz. İkinci adımda, üretim proseslerimizi ve bu proseslere ait verilerin çizimi yapılmalıdır. Prosesleri temsilen proses kutuları kullanılır. Proses kutularının hemen altında başlangıçta topladığımız (çevrim süresi, kurulum süresi, makine kullanım oranı vb.) bilgiler girilir. Ara stokları üçgen şeklinde gösteririz ve stoklar size prosesin nerede başlayıp nerede bittiğini gösterdiği için önem taşır. Üçüncü adımda ise, tedarikçiler ve sağladıkları malzemenin verileri girilmektedir. Kamyon (kullanılıyorsa farklı taşıtlar da olabilir) ve kalın ok ile tedarikçiler ve müşteriye ulaşımı çizilir. Dördüncü adımımız, bilgi akışının çizilmesi ile gerçekleşir. İnce çizgiyle gösterildiği gibi, eğer ki elektronik ortam ile sağlanıyorsa şimşek şekline benzer bir çizgiyle gösterilir. Beşinci ve son adımımızla, ürünün malzeme tedarikçilerinden başlayarak, müşteriye ulaşıncaya kadarki geçirdiği sürecin süresinin hesaplanması gerçekleştirilir. Burada zaman ekseni çizimi yapılır. Ayrıca katma değer süresi, proses çevrim verimliliği gibi hesaplamalar ile haritamız tamamlanmış olur. Aşağıda bir mevcut durum haritası görmektesiniz.
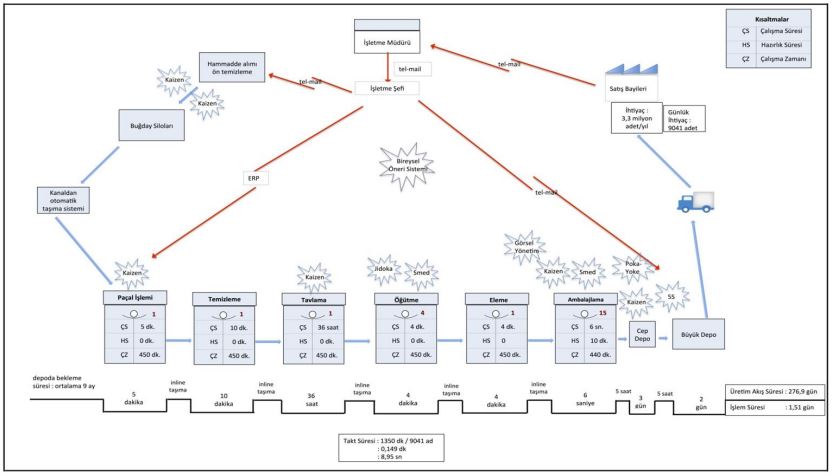
3) Gelecek Durum Haritası
Mevcut durum haritasından kazanımlar çıkarma vakti diyebiliriz. Artık iyileştirme için neler yapmamız gerektiğinin bilgisine ulaşarak, ideal duruma varasıya kadar gelecek durum haritası çıkarılmalıdır. Gelecek durum haritası, yapılan iyileştirmeler sonucunda mevcut duruma dönmektedir. Buna sürekli iyileştirme diyoruz.
Gelecek durum haritası çıkarmak için gerekli adımlara gelecek olursak eğer, takt zamanı hesaplamakla başlamalıyız. Takt zamanını, toplam kullanılabilir zamanın müşteri talebine oranı şeklinde açıklayabiliriz. Eğer dikkat edersek yukarıda mevcut durum haritası çiziminde de ilk müşteriye odaklanmıştık. Burada da yine müşteriyle başladık. Çünkü değeri müşteri bazlı düşünmeliyiz. Müşterinin gerçekten de neye ihtiyacının olduğu irdelenmeli. İsrafa neden olan adımları ya da etkileri ortadan kaldırma gibi iyileştirme çalışmalarına göre haritamızı şekillendirmeliyiz.
Sürekli akışın sağlanması ve esnek üretim yapılması sağlanmalı. Sürekli akış sağlayamadığınız yerde süper marketleri dahil edebilirsiniz.
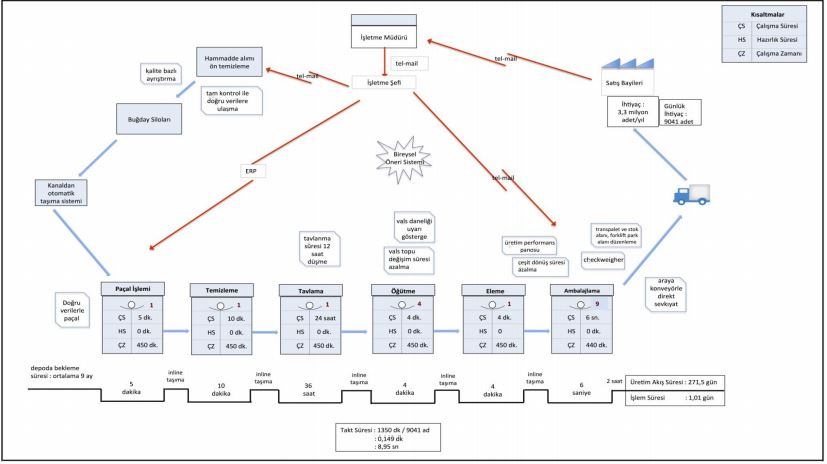
4) Değer Akış Planı ve Uygulama
Artık elimizdeki haritalardan elde ettiğimiz çıkarımları uygulamaya koyma vaktidir. Yapacak olduğumuz iyileştirmelerin tamamını aynı anda gerçekleştirmek mümkün olmayabilir. Bu nedenle tam olarak nereden başlayacağımıza karar vermeli ve iyileştirmelerin her birinin ne kadar süre alacağını, maliyetinin ne kadar olacağı, bu iyileştirmelerden kimlerin sorumlu olacağı, hedeflenen değişimlerin ne olacağı gibi bazı ayrıntılar artık tam anlamıyla şekillenmelidir.
KAYNAKÇA
https://asq.org/quality-resources/lean/value-stream-mapping
https://lean.org.tr/uretimde-deger-akis-haritalama-gormeyi-ogrenmek-kitabinin-ozetidir/
Aydın, Hakan. “Yalın Üretim Sistemi, Değer Akış Haritalama Yöntemi Ve Yalın Üretim Sisteminin Çalışanlara Etkileri Yüksek Lisans Tezi” . Marmara Üniversitesi Sosyal Bilimler Enstitüsü İşletme Anabilim Dalı Uluslararası Kalite Yönetimi Bilim Dalı, (2009)
Sarucan, Ahmet – Yılmaz Ahmet “Değer Akış Haritalama Süreci Ve Bir İşletmede Uygulama”. Uluslararası Sosyal ve Beşeri Bilimler Araştırma Dergisi, (2019)
Birgün, Semra – Gülen, Güven, Kemal – Özkan, Kadriye “Yalın Üretime Geçiş Sürecinde Değer Akışı Haritalama Tekniğinin Kullanılması: İmalat Sektöründe Bir Uygulama”. İstanbul Ticaret Üniversitesi Fen Bilimleri Dergisi, 9 (2006) , 47-59.
Sarı, Bilgin, Emre “Üretim Hattı Tasarımında Değer Akış Haritalama Tekniğinin Kullanılması “. Dumlupınar Üniversitesi Sosyal Bilimler Dergisi, 56 (2018)